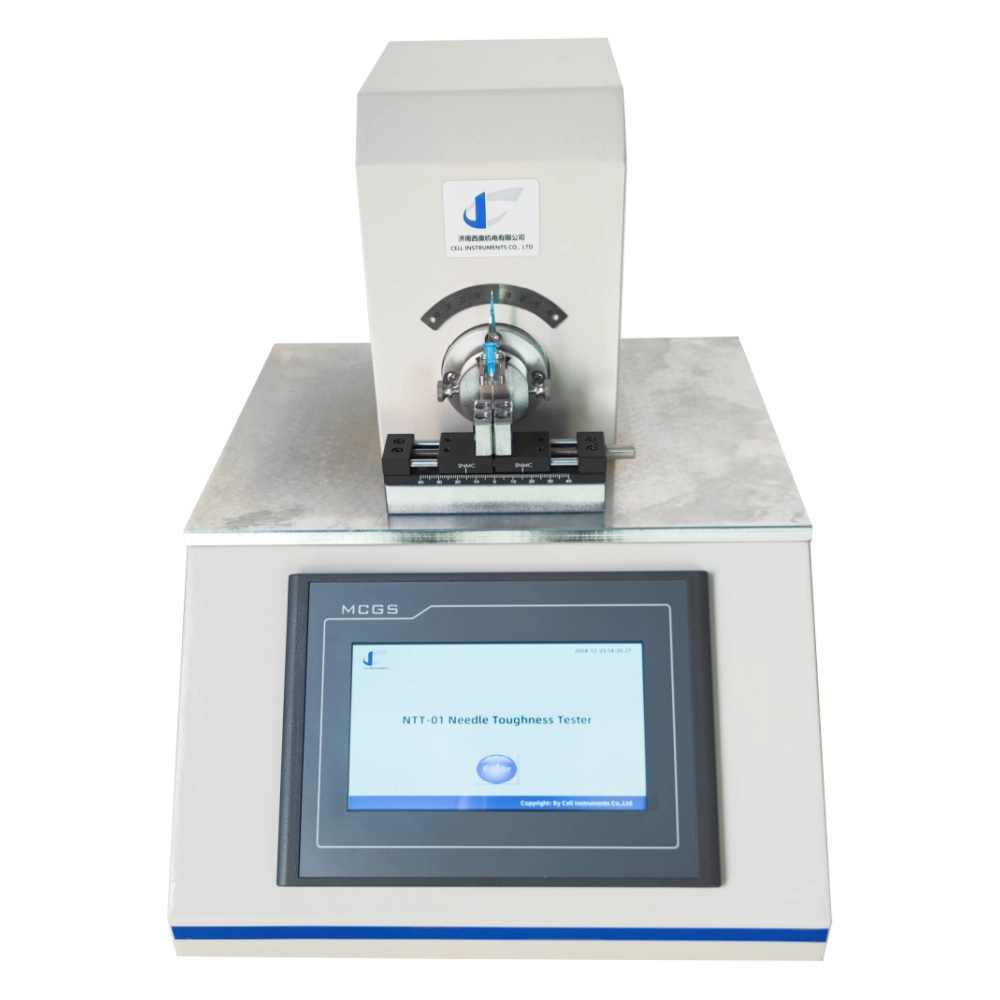
For medical device, ensuring the quality and safety of hypodermic needles is crucial. One of the key tests used to assess the durability of these needles is the medical needle break resistance tester. This test evaluates the ability of needles to withstand mechanical stress during insertion and withdrawal.
What Is Medical Needle Break Resistance Tester?
A medical needle break resistance tester is a specialized instrument designed to evaluate the breakage resistance of hypodermic needles. It works by simulating the forces applied to needles during use, particularly the bending forces that occur when a needle is inserted or withdrawn. The test involves applying a controlled force to bend the needle at specific angles and observing its ability to resist breakage.
The primary function of this tester is to verify that needles can withstand normal mechanical stresses without breaking or deforming. This ensures that medical professionals can rely on the needles during procedures, reducing the risk of injury or device failure.
ISO 9626 Standard for Needle Testing
ISO 9626, a critical international standard for the design and testing of medical needles, provides guidelines on the mechanical properties of needles, including their resistance to breakage. Specifically, ISO 9626 Annex C outlines the testing procedures for assessing the tubing’s resistance to breakage through bending.
ISO 9626 Testing Requirements
According to ISO 9626, the medical needle break resistance tester must apply a force to bend the needle (or tubing) at a specified distance from the fixed end. The needle should bend through angles of 25° for regular-walled tubing, 20° for thin-walled tubing, and 15° for extra-thin-walled or ultra-thin-walled tubing. This bending is done both in one direction and then in the reverse direction, simulating the stress experienced during actual use.
The test is performed in cycles, typically 20 complete cycles, with a frequency of 0.5 Hz. The needle is then visually inspected for signs of breakage or deformation. If the needle survives the bending test without breaking, it is deemed suitable for use in medical applications.
Medical Needle Break Resistance Tester Principle
The medical needle break resistance tester operates by fixing one end of the needle or tubing in place, while a force is applied at a specified distance. The force bends the needle in one direction and then reverses the force to bend it back, simulating the stresses experienced during real-life use.
The main components of a needle break resistance tester include:
- Support system: Holds the needle securely in place during the test.
- Force application system: Applies the required bending force at the specified distance.
- Control system: Allows for the precise adjustment of test parameters such as bending angle, frequency, and cycles.
- Visual inspection system: After the test, the needle is visually inspected for any visible breakage or deformation.
ISO 9626 Annex C: Detailed Testing Procedure
ISO 9626 Annex C provides a clear and comprehensive procedure for testing the resistance of hypodermic needles to breakage. This annex includes specifications for the bending angle, the frequency of cycles, and the method for visually inspecting the needle after testing.
Testing Procedure According to ISO 9626 Annex C
- Fix the tubing: One end of the needle is securely fixed in the support device.
- Apply the bending force: A force is applied to bend the needle at a specific angle—25° for regular-walled needles, 20° for thin-walled needles, and 15° for extra-thin-walled needles.
- Reverse the force: The force is applied in the opposite direction to bend the needle back.
- Complete cycles: The bending force is applied for 20 complete cycles at a frequency of 0.5 Hz.
- Inspection: After testing, the needle is visually inspected for any breakage or deformation.
Test Results and Documentation
After completing the test, the results are documented, including:
- The needle type (regular-walled, thin-walled, etc.).
- Any visible signs of breakage.
- The date of testing.
- The material and dimensions of the needle.