Understanding Hydrolytic Resistance in Glass Containers for Pharmaceuticals
The pharmaceutical industry relies heavily on glass containers for the packaging and preservation of various products. These containers must possess certain qualities to ensure that they keep their contents safe and unchanged over time. One such quality is hydrolytic resistance – an essential characteristic that ensures that pharmaceuticals remain unaffected by reactions with the glass material. This article delves into the details of hydrolytic resistance, the process of testing for it, and the reasons behind the treatments applied to glass containers.
Glass Containers for Pharmaceutical Applications
Glass containers intended for pharmaceutical purposes are engineered to be in direct interaction with medicinal products. The types of glass employed for these containers fall into two categories: borosilicate glass, also known as neutral glass, and soda-lime-silica glass. Borosilicate glass boasts a composition rich in boric oxide, aluminum oxide, and alkali or alkaline earth oxides, contributing to its exceptional hydrolytic resistance and formidable resilience against thermal shocks. This type of glass is recognized as Type I due to its characteristics.
On the other hand, soda-lime-silica glass, a variant of silica glass, predominantly comprises alkaline metal oxides, especially sodium oxide, and alkaline earth oxides, namely calcium oxide. The inherent chemical makeup of this glass grants it a moderate level of hydrolytic resistance, categorizing it as Type III. However, treating the internal surface of soda-lime-silica glass containers enhances their hydrolytic resistance, lifting them to a Type II classification.
Optimal Glass Type Selection for Pharmaceutical Containers
Considering hydrolytic resistance test outcomes, certain guidelines are proposed for selecting the appropriate glass for pharmaceutical containers. Type I glass containers are universally compatible with a vast array of parenteral and non-parenteral products. Type II varieties are ideal for acidic and neutral aqueous products for both parenteral and non-parenteral uses and can suit alkaline parenteral products when stability studies affirm their compatibility. Meanwhile, Type III glass vessels are generally not recommended for parenteral applications or powder forms intended for parenteral usage unless stability testing verifies their adequacy.
Enhancing Hydrolytic Resistance by Treating Interior Glass Surfaces
Improving the hydrolytic resistivity of glass containers is often achieved through treatments to their inner surface. Simultaneously, exterior surface treatments are employed to lessen friction and shield the container against abrasion and breakage risks. Such external treatments are executed in a way that preserves the pristine condition of the container’s inner surface.
Hydrolytic Resistance Apparatus
Effective hydrolytic resistance testing involves using a mortar and pestle system, specifically a hardened-steel variant, to crush glass into fine grains. To accompany this, there is a necessity for a series of stainless steel square-mesh sieves framed with US Sieve Nos. 25, 40, and 50, and a shaking device for mechanical sieving. Additional apparatus include a magnetic steel hammer, a magnet, weighing containers, stoppers, metal foils, a temperature-controlled oven, a precision balance, a desiccator, and an ultrasonic bath – all vital components of the glass grain hydrolytic resistance testing process.
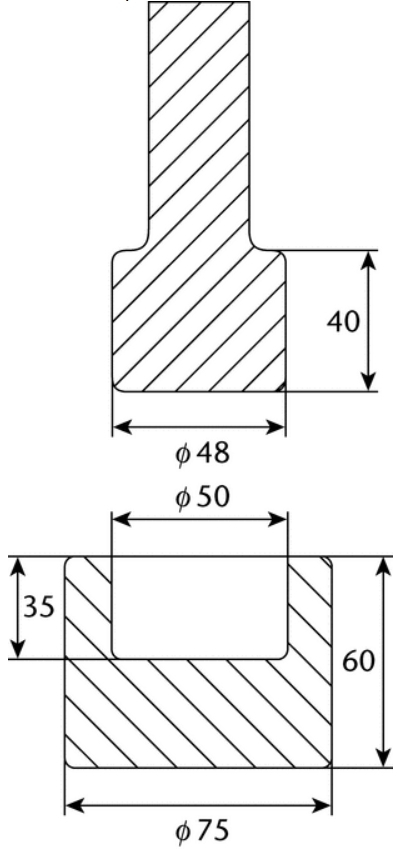
The Mortar and pestle for pulverizing glass
Innovations in Hydrolytic Resistance Testing: The GHR-01A Glass Grain Hydrolytic Resistance Sampler
The GHR-01A Glass Grain Hydrolytic Resistance Sampler exemplifies modern engineering tailored for assessing glass grain hydrolytic resistance in medical glass items like infusion bottles, ampoules, and oral liquid containers. Its intelligent design affords a highly automated process for the pulverization and screening of glass grains, elevating the level of automation within such equipment.
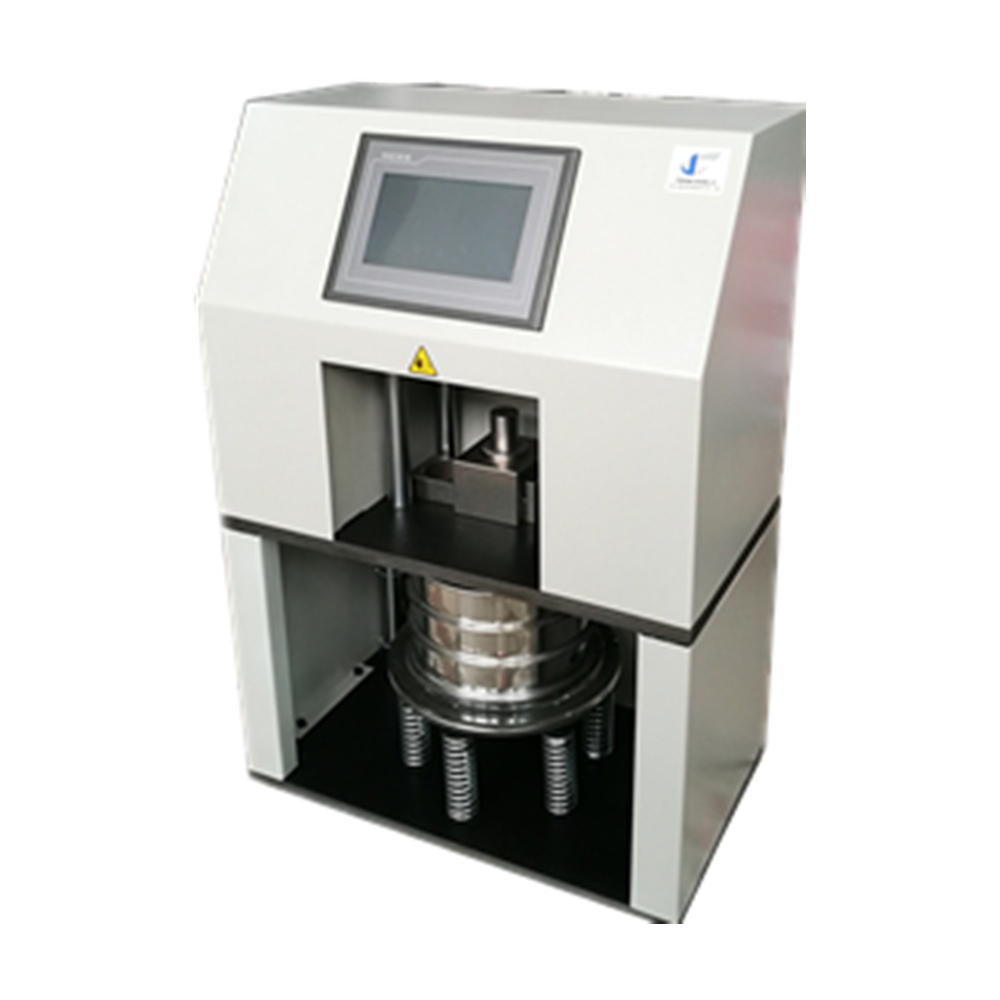
The GHR-01A Glass Grain Hydrolytic Resistance Sampler
Download its Catalog
Instrumentation Innovation in Hydrolytic Resistance
The GHR-01A Glass Grain Hydrolytic Resistance Sampler Provide below benefits for Users
- A synergy of intelligent automation functions simplifies the process, autonomously streaming samples to specific sizes per industry standards.
- A user-friendly liquid crystal interface fosters straightforward interactions between the user and the device.
- Automation minimizes the need for manual handling, amplifying safety and ushering better protective measures.
- Protective features are integrated to contain glass shards, ensuring a contaminant-free test environment.
- The embedded system deploys a safe methodology for collecting and disposing of glass residues.
- Automated sieving escalates the accuracy of test results by offering precise vibratory filtering.
- For enhanced safety, a limit switch provides added automated protection.
- Sturdy vertical design counteracts gravity’s impact on the sample analysis, a boon when dealing with substantial sample sizes.
Ensuring Quality and Compliance Through Hydrolytic Resistance
To ensure the highest quality and safety standards, glass containers must undergo rigorous hydrolytic resistance testing. It is not only a measure of the glass’s performance but also a testament to the pharmaceutical industry’s commitment to delivering safe and reliable products to consumers.
Sustainability in Hydrolytic Resistance Testing
Evaluating the hydrolytic resistance of glass containers plays a crucial role in sustainable packaging practices. As the industry gravitates towards more eco-conscious methods, it becomes imperative to balance environmental considerations with the need for preserving the integrity of pharmaceutical products.
Concluding Reflections on Hydrolytic Resistance in Glass Packaging
Hydrolytic resistance is a cornerstone of glass container integrity for pharmaceuticals, affecting the stability and overall quality of the products enclosed. Advancements in testing equipment like the GHR-01A Glass Grain Hydrolytic Resistance Sampler have set new benchmarks for the industry, ensuring that the hydrolytic resistance of glass is both measurable and manageable. The evolution of treatments and coatings for glass containers continues to adapt to the changing needs of pharmaceutical storage, maintaining an invaluable balance between durability and drug efficacy. As we progress, the ongoing research and development in this field are pivotal to the ceaseless pursuit of exemplary pharmaceutical packaging solutions.
International Standards for Glass Grain GHydrolytic Resistance Sampling
ISO 719 and ISO 720, alongside USP 660, are critical standards that establish guidelines for assessing the hydrolytic resistance of glass grains, crucial for pharmaceutical container manufacturers. ISO 719 provides the methodology for determining the hydrolytic resistance of glass at 98 degrees Celsius, offering a measure of the glass’s durability when in contact with water. ISO 720 outlines the procedure for testing at a lower temperature of 121 degrees Celsius, typically used for autoclave resistance analysis. USP 660 details the requirements for physicochemical tests related to the hydrolytic resistance of glass used in pharmaceutical products, ensuring the material’s consistency and reliability for medication safety.
Luer Cone Breakage Resistance – ISO 11040-4 Annex C2
Flange Breakage Resistance – ISO 11040-4 Annex C1
Syringe Leakage Testing – ISO 11040-4 Annex G2
Needle Bonding Strength Test ISO 11040-4 Annex G1
Syringes Needle Penetration Test ISO 11040-4 Annex F
Bloom Strength of Soft Gelatin Capsules
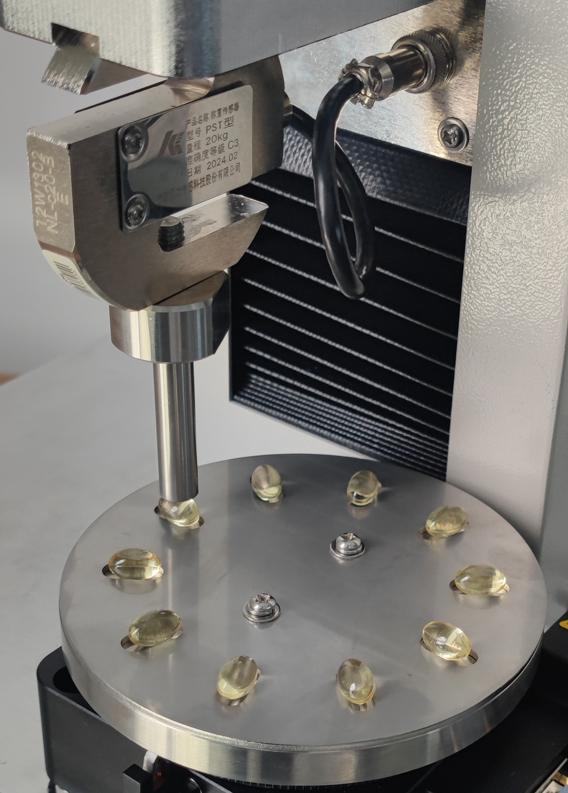
The Continuous Softgel Feeding System
A ten sample positioning plate of auto rotating design to improve test efficiency and save labor